Oil – Why Understanding Where it Comes From is Important (2)
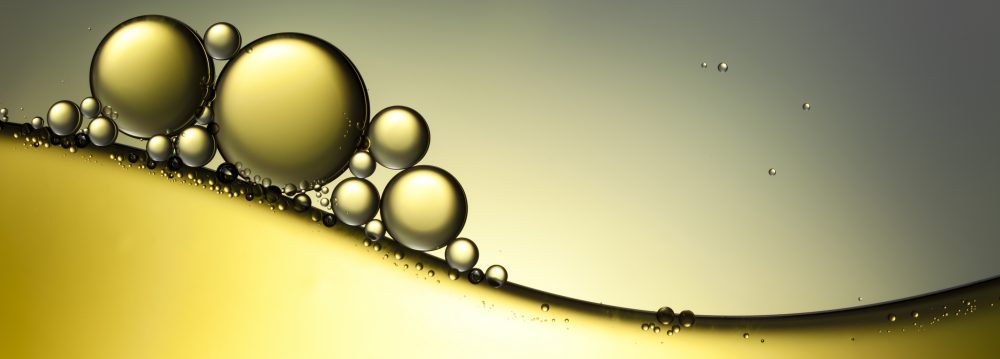
The Origins of Oil
In a previous post we explored where and how oil originates from a geological perspective, taking a look at the origin of fossil fuels, the conditions under which they developed, the types of rocks and minerals involved in their production and the processes of energy exploration and extraction. In this second round we’ll dive into the refining process and breakdown what manufacturers produce from a barrel of oil as an end product.
Fossil Fuels and Oil – The Product of Heat and Pressure
As with the initial development of fossil fuels, their refinement into viable products is entirely dependent upon both heat and pressure. Depending on how much heat you apply to crude oil, it’s volatility and the molecular structure of its hydrogen-carbon molecules will become more stable for use in higher heat applications. In general, a lower temperature refining process will result in cokes while higher temperatures will give you a gas. The following processes are integral parts of the initial refining process:
- Hydrotreating – The process of reducing sulphur, nitrogen and aromatics (produced by fluid catalytic cracking of petroleum fractions) to enhance density, smoke point and cetane number (a fuel’s ignition properties and delay, which is the time between fuel injection and the initial pressure increase during combustion).
- Hydrocracking – The hydrogenated catalytic chemical process that converts high-boiling hydrocarbons found within crude oil into products such as gasoline, diesel, fuel, jet fuel and kerosene, which have a lower boiling point and are more valuable. The process of hydrocracking turns heavy crude into lighter, more usable products.
- Hydroprocessing – The process of removing contaminants from crude such as sulfur, nitrogen, olefins and aromatics.
Solvent Extraction and Processing
Starting with a parrafinic base oil, solvent processing is used to further refine lubricant products to higher levels of quality and to create a spectrum of viscosity for different applications and temperatures. With solvent extraction, aromatics and other impurities are removed to minimize oxidation and to stabilize the oil to accommodate varying temperatures, which can remove between 50-80% of unwanted components and impurities. The viscosity (thickness) of the aromatic components in a base oil determine a lubricant’s ability to accommodate fluctuations in temperature and provide adequate film thickness in both hot and cold climates and application environments.
The Viscosity Index (VI) illustrates a lubricant’s ability to respond to temperature fluctuations with the higher the “VI,” the lower the change of oil viscosity in relation to temperature and the lower the ranking along the viscosity index, the greater the change in viscosity. Solvent dewaxing is another important part of the refining process, whereby wax is removed from a base oil to keep it from crystallizing within an engine in lower temperatures.
Base Oils and Additives
Certain additives significantly alter the composition of finished end products, giving you greases, gear oils, diesel fuel and the differentiation of fuel grades depending on additive-to-base oil ratio. In 1947, the American Petroleum Institute (API) began categorizing oils by their degree of service within an engine – regular, premium or heavy-duty. Premium and heavy-duty engine oils began to be additized to extend their life for what was considered “severe applications” in the commercial and industrial sectors and to extend performance in fluctuating temperatures. The API also developed Base Stock Categorization, the grouping of base oils into groups I, II, III, IV and V depending on sulfur composition, weight, the percentage of saturates and an oil’s viscosity index rating.
API Base Groups
The American Petroleum Institute categorizes lubricant base oils derived from fossil fuels into 5 Groups according to API 1509, Appendix E. The first three categories are initially refined from crude oil and are mineral based, Group IV polyalphaolefin oils are fully synthetic and Group V oils combine all base oils not recognized in Groups I thru IV. Before additives are included to create a specific lubricant formulation, all base oils fall under one of the 5 API Group categories. All formulations depend on the percentage of saturates, sulfur, weight and where they lie on the viscosity index.
- Group I – The least expensive base oils on the market, Group I oils are solvent-refined and have a temperature range between 32 to 150 degrees F. Containing less than 90% saturates, more than 0.03% sulfur and a viscosity index range of 80-120.
- Group II – The most used oil on the market for their affordable price comparable to Group I oils, Group II base oils are produced via hydrocracking and have a viscosity index of 80-120. Less than 0.03% sulfur and more than 90% saturates, it’s more translucent in color and has hydrocarbon molecules that are saturated, so they tend to have better antioxidation capabilities.
- Group III – Becoming increasingly prevalent in the market, Group III base oils are hydrocracked with a viscosity index of 120. 90% saturates and less than 3% sulfur, Group III oils are derived from minerals but are often described as possessing synthetic hydrocarbons because of their purity based on an extended refining process under extreme heat and pressure.
- Group IV – Manufactured in petrochemical refineries, polyalphaolefins (POA’s) are made through the process of “synthesizing” and begin with the production of ethylene, the feedstock for a myriad of plastic materials. In order to make a quality synthetic base, ethylene is reacted with specific catalysts and combined under considerable pressure with additional catalysts and hydrogen, creating larger molecules with end results that are high quality and can accommodate a broader temperature range and more extreme applications. POA’s in Group IV are more thermally stable, have a higher viscosity index, better volatility and lower temperature fluidity than other groups.
- Group V – This group of base oils includes all other bases such as esters, polyester and silicone. Often combined with other base oils to create different lubricant formulations that improve the properties of the existing base oil, such as extending usage and making a product more capable of accommodating greater temperature fluctuations.
What A Barrel of Oil Becomes
According to the website GasBuddy and an Energy Information Administration (EIA) 2013 study, a 42-gallon barrel of crude oil creates 45 gallons of petroleum products. Roughly 47% of each barrel of crude oil is ultimately refined into gasoline for automobile use. In the United States, roughly 2.5 gallons of crude oil are consumed per person, per day and the US imports approximately 40% of its required crude oil with about 52% of that volume coming from the Organization of the Petroleum Exporting Countries (OPEC), an intergovernmental organization founded in 1960. The breakdown of additional products per barrel of oil are as follows:
- Gasoline – 47%
- Heating Oil/Diesel Fuel – 20%
- Jet Fuel (Kerosene) – 8%
- Propane/Propylene – 6%
- Natural Gas Liquids and Liquid Refinery Gases – 6%
- Still Gas 4%
- Petrochemical Feedstocks – 2%
- Petroleum Coke – 2%
- Residual Heavy Fuel Oil – 2%
- Asphalt and Road Oil – 2%
- Lubricants – 1%
- Miscellaneous Products – 0.4%
- Other Liquids – 0.4%
- Aviation Gasoline – 0.1%
- Special Napthas – 0.04%
- Waxes – 0.04%
- Kerosene – 0.02%
Contact an SCL Consultant today
In a wide range of industrial sectors, if there’s metal touching metal, oil is involved. At SCL, we’re here to protect and optimize the machines that keep our country moving and we pride ourselves on providing superior logistics and solutions, extensive product and industry knowledge and total performance satisfaction for our customers. Understanding the story and best-practice application of a wide spectrum of petroleum products is our job, and we hope you enjoyed this second article about the refinement of fossil fuel and petroleum products. For information on how we can assist your fleet in choosing the optimal products at a competitive price, contact an SCL consultant today.