Reliability-Centered Maintenance Programs For Your Business
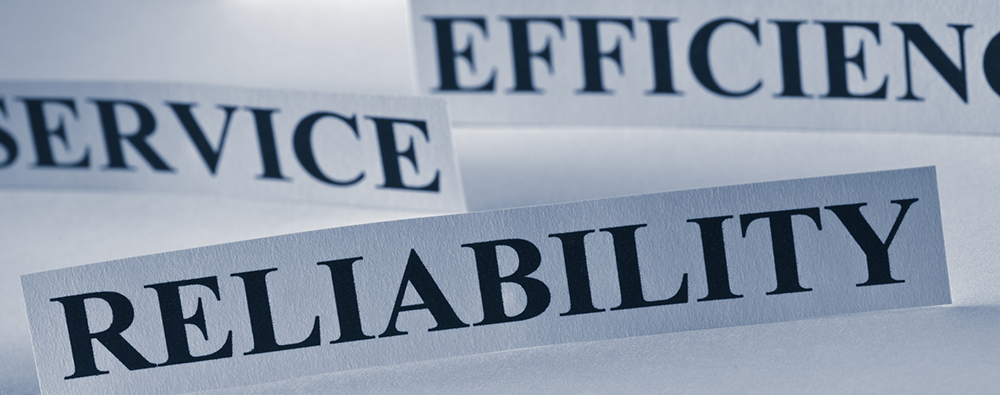
Reliability-Centered Maintenance Programs
Protect Your Physical Assets with Reliability-Centered Maintenance Programs
Reliability-Centered Maintenance (RCM) is an engineering framework that allows for the creation of a complete maintenance regimen for your physical assets to understand the overall level of risk being managed by an organization. The idea of Reliability-Centered Maintenance Programs has been around since the 1970’s, first coined by senior executives and engineers at United Airlines, who outlined a process whereby the company could determine optimum maintenance requirements for their aircraft in order to ensure the highest level of safety and performance. This public document was later adapted by the U.S. Department of Defense into a textbook and evaluation report, which introduced the idea of RCM to a greater audience. In 1991, John Moubray published the book, Reliability-Centered Maintenance, which further expanded the concept to businesses, organizations and industries, such as the U.S. military, the U.S. commercial nuclear power industry, Boeing, and the Walt Disney Company, among others.
What Is Reliability-Centered Maintenance
RCM is described as being a process that outlines user requirements for maintaining efficient system operations. It is implemented to define safe minimal levels of maintenance to increase:
- Cost effectiveness
- Reliability
- Machine uptime
According to author John Moubray, “RCM is rapidly becoming fundamental to the practice of maintenance management and is now in use at hundreds of industrial and service organizations around the world. It is of vital importance to anyone concerned with productivity, quality, safety, and environmental integrity.” In his book, Moubray outlines how RCM can impact condition monitoring, the analysis of functions and failures, the inevitability of human error, and much more. RCM is a cost-effective routine maintenance option that highlights the most pressing causes of equipment failure, utilizing predictive maintenance analysis and techniques to keep a tight ship running at optimal productivity.
How RCM Works
Defined by the technical RCM standard SAE JA1011, Evaluation Criteria for RCM Processes, a minimum criteria has been established that any process should meet before it can be considered a Reliability-Centered Maintenance program. The seven questions below are part of the evaluation criteria that determines whether or not a process is RCM compliant:
- 1. What is the item supposed to do and its associated performance standards?
- 2. In what ways can it fail to provide the required functions?
- 3. What are the events that cause each failure?
- 4. What happens when each failure occurs?
- 5. In what way does each failure matter?
- 6. What systematic task can be performed proactively to prevent, or to diminish to a satisfactory degree, the consequences of the failure?
- 7. What must be done if a suitable preventive task cannot be found?
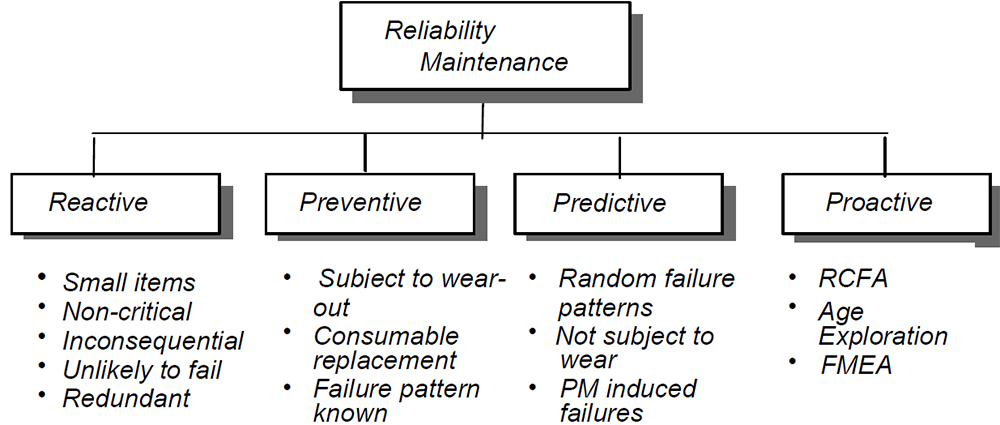
Reliability-Centered Maintenance Flow Chart
RCM Risk Management Potential
Reliability-Centered Maintenance focuses on identifying and minimizing three primary risks, or threats:
- Safety
- Operations
- Overall organizational maintenance budget
Threats to the environment occupy their own classification, although are generally regarded in the same way as threats to safety. Following a list of risk management strategies, RCM seeks to mitigate risk through the following strategies:
- Predictive maintenance tasks
- Preventive Restoration or Preventive Replacement maintenance tasks
- Detective maintenance tasks
- Run-to-Failure
- One-time changes to the “system” (such as changes to hardware design or to operations)
The Future of RCM
As companies strive more and more to save money, implementing leaner and more cost effective operations, they often lack personnel or resources to successfully operate from an RCM initiative. Multiple would-be RCM programs have popped up over the years, claiming to provide the same structure and reliability to companies, but they are greatly watered down versions of the original programs designed by the aviation and defense industries to ensure optimal safety and integrity. For more information on how your company can introduce Reliability-Centered Maintenance Programs within your business, read John Moubray’s, Reliability-Centered Maintenance, or read through the SAE standards. The standards outlined allow for heightened asset management, safety, and an overall increase in productivity and efficiency, which positively impacts a company’s bottom line.
Contact an SCL Consultant Today
In a wide range of industrial sectors, SCL is committed to being the number one logistics and solutions provider for the products that protect and optimize the machines that keep our country moving. We pride ourselves on remaining at the forefront of industry trends and technological innovations, and as the market continues to evolve, we are committed to providing extensive product and industry knowledge and total performance satisfaction for our customers. For information on how we can assist your fleet in choosing the optimal products at a competitive price, contact an SCL consultant today.